Impeller – Vaned Diffuser Interaction In A Centrifugal Compressor
Test At Design and Off Design Conditions
The experimental work was performed at the LFM of Energy Dept. of the Politecnico di Milano, on a closed loop test rig for compressors and turbines. The test campaign was carried out in the centrifugal section using air as working gas and imposing the ambient pressure at the stage inlet. The tested impeller is a centrifugal transonic unshrouded rotor with a radial discharge section. The diffuser height being greater than the impeller blade one, the configuration is at smoke-shelf at the tip side .
The test rig is instrumented to allow overall performance measurements and detailed analysis of the flow within the impeller, at the impeller discharge and within the diffuser. In order to allow impeller – vaned diffuser interaction analyses, the diffuser can be rotated by a stepping motor. The diffuser discharges the flow in a volute characterised by a rectangular section that acts as a plenum. The measurements have been taken by means of a FRAPP at four different radial positions, for 15 tangential positions on the diffuser pitch and for 12 points on the blade height.
The compressor head was measured by two transducers connected to pressure taps at the inlet and outlet of the machine; the flow rate was measured by a Venturi nozzle manufactured according to the EN ISO 5167-3 standard. The rotational speed was taken by a pick-up located on the compressor shaft; the same device was used as key-phasor for the phase-resolved measurements. Steady temperature measurements in the vaneless diffuser were taken by a total temperature Kiel probe, which implemented a T type thermocouple.
As centrifugal compressors find a huge number of applications in industry and in aero-engine, the detailed analysis and comprehension of the impeller – vaned diffuser interaction is of interest to improve the efficiency and the operating range. A wide experimental campaign devoted to the understanding of the impeller – diffuser interaction is carried out; in particular the work focuses on the features occurring when the compressor works in off design conditions. Data were taken at 3 operating points (near surge, best efficiency and maximum flow rate point) in the impeller - vaned diffuser gap by a fast response probe; the single stage compressor runs at 12500 RPM giving peripheral Mach number of 0.77.
At first, data are reduced to evidence the main impeller flow features which are compared at different flow rates. Furthermore time mean diffuser effects on the impeller are commented and finally the impeller - diffuser interaction is discussed. Results evidence the effect of the diffuser on the impeller, mainly in terms of static pressure and flow velocity, which have a strong dependence on the flow rate.
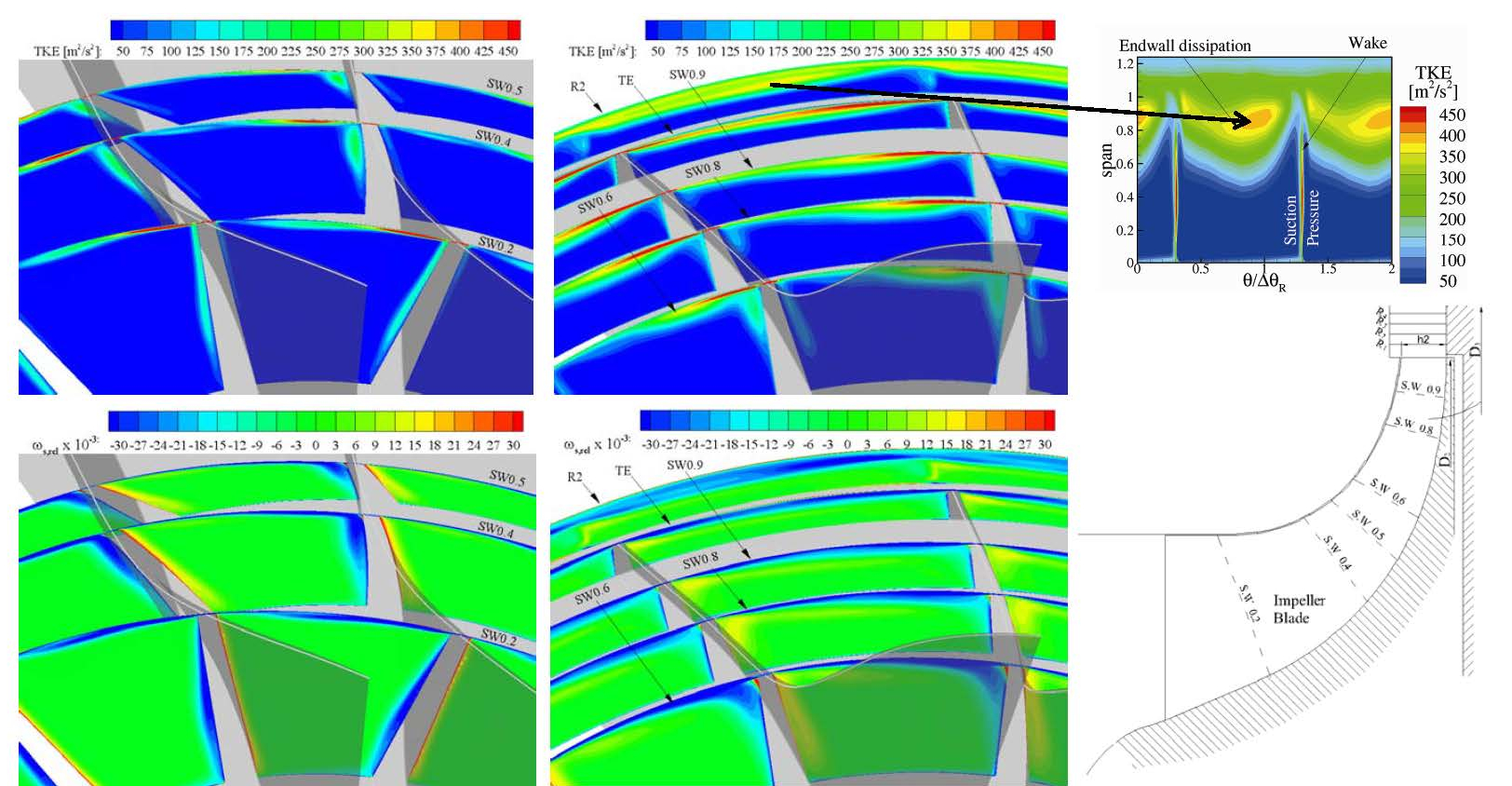
Impeller time-mean aerodynamics: Flow development inside the rotor channel (CFD)
-
-
Strong TKE (top) development on SS and SS/tip corner ends up in blade wake
-
High negative ωs (bottom) on the SS and SS/tip corner, weak positive ωs confined on PS
-
High viscous activity on the tip-SS corner marks TLV development, only vortex structure
-
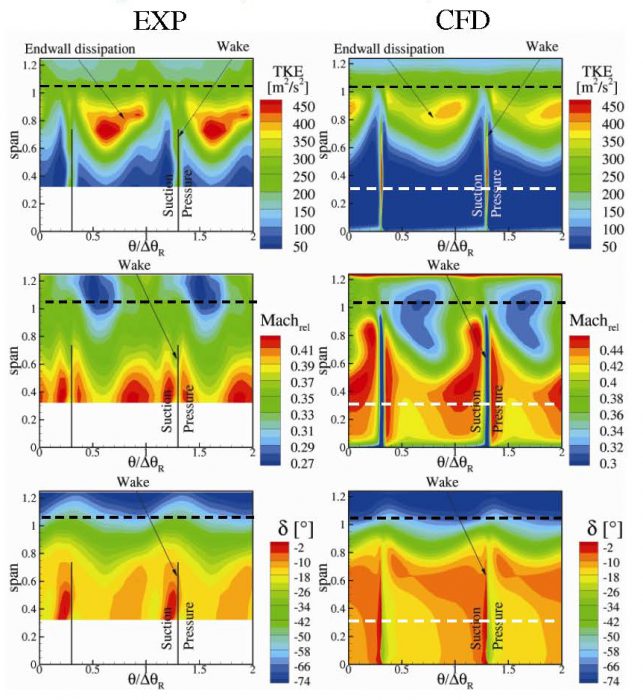
Impeller time-mean aerodynamics: Relative flow field in rotating frame (EXP & CFD)
-
-
Good EXP-CFD agreement
-
Narrow wake and wide endwall dissipation assessed as main viscous features
-
Endwall loss around midpich (depends on tip clearance)
-
At mid/hub wide free-stream interrupted by narrow wakes
-
Mrel dominated by impeller blade potential effects
-
δ dominated by impeller blade potential field
-
No trace of vortex structures
-
Very high slip at the shroud, enhanced by smoke-shelf (reversed flow)
-
Impeller – diffuser interaction
Unsteady flow field in the vaneless diffuser to discuss the impeller-diffuser interaction -- Focus on pitch-stream-wise planes at fixed span, representative of most blade height < 80%
Turbulent Kinetic Energy
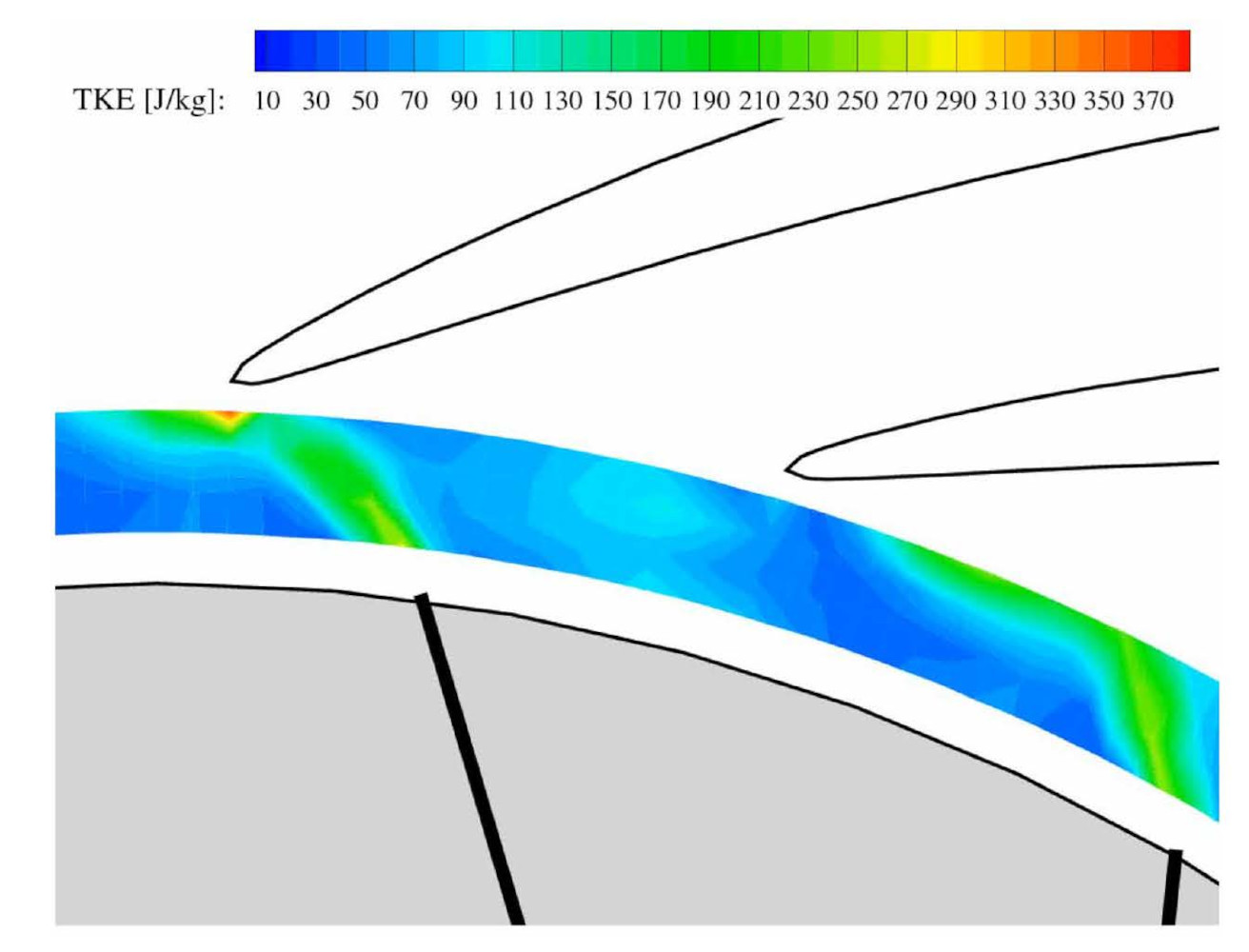
Static Pressure
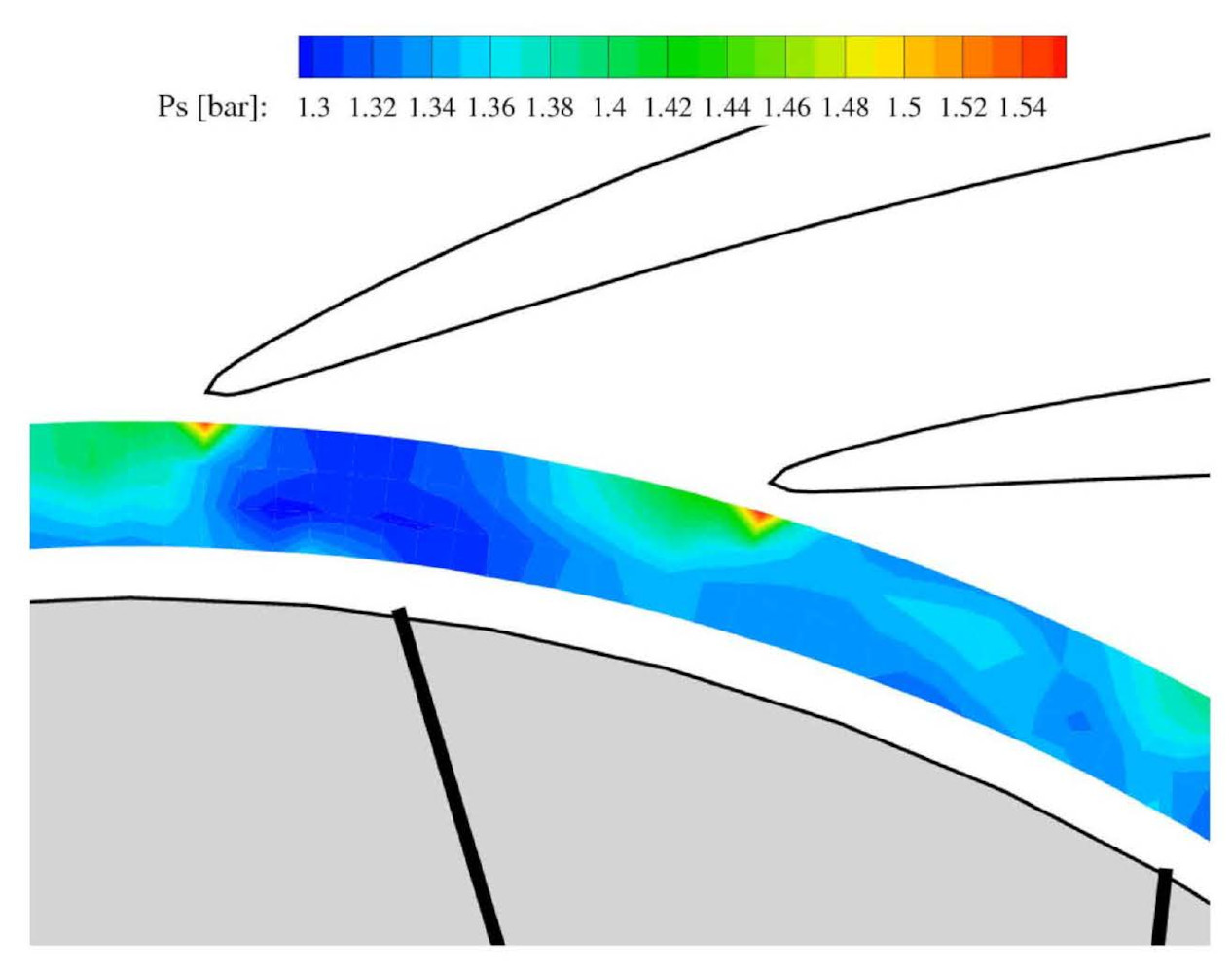
Mach Number
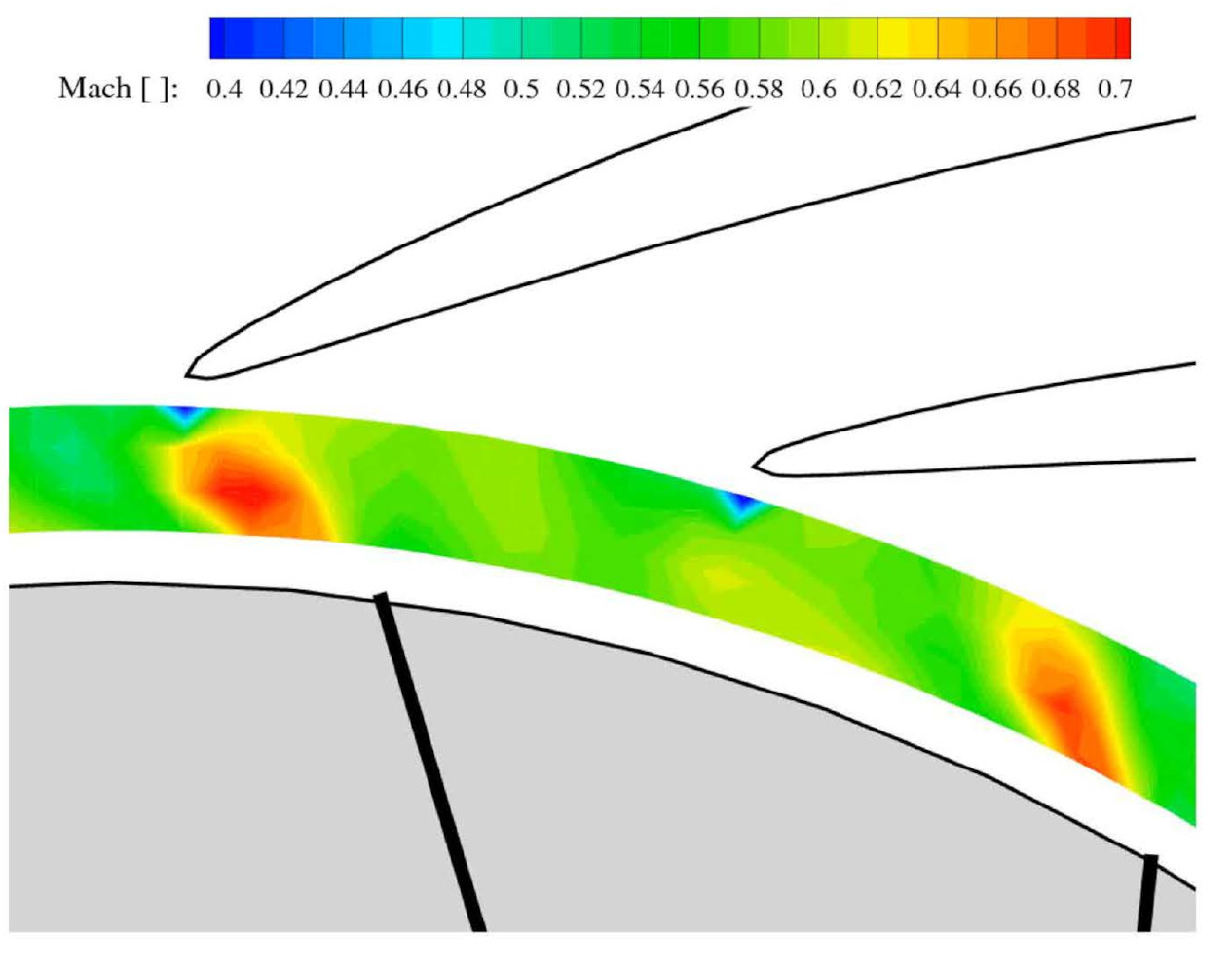
Selected References
-
Persico G., Gaetani P. Guardone A., 2005 "Dynamic calibration of fast-response probes in a low pressure shock tube", Meas. Sci. Technol. Vol. 16 (2005), pp 1751-1759
-
L. Toni, V. Ballerini, S. Cioncolini, P. Gaetani, G. Persico, “Unsteady Flow Field Measurements in an Industrial Centrifugal Compressor” 39th Turbomachinery Symposium - October 4-7, 2010 – Houston, Texas
-
P. Gaetani, G. Persico, A. Mora, V. Dossena, C. Osnaghi “Impeller – vaned diffuser interaction in a centrifugal compressor at the best efficiency point”,Vancouver, ASME GT2011-46223, Proceedings of ASME Turbo Expo 2011: Power for Land, Sea and Air, June 6-10, 2011, Vancouver, Canada.
-
P. Gaetani, G. Persico, A. Mora, V. Dossena, C. Osnaghi “Impeller – vaned diffuser interaction in a centrifugal compressor at off design conditions”, Vancouver, ASME GT2011-46234, Proceedings of ASME Turbo Expo 2011: Power for Land, Sea and Air, June 6-10, 2011, Vancouver, Canada.
-
E. Guidotti, L. Tapinassi, L. Toni, L. Bianchi, P. Gaetani, G. Persico “Experimental and numerical analysis of the flow field in the impeller of a centrifugal compressor stage at design point”, Vancouver,ASME GT2011-45036, Proceedings of ASME Turbo Expo 2011: Power for Land, Sea and Air, June 6-10, 2011, Vancouver, Canada.
-
P. Gaetani, A. Boccazzi, R. Sala, “Low Field in the Vaned Diffuser of a Centrifugal Pump at Different Vane Setting Angles” J. Fluids Eng. 134, 031101 (2012)
-
P. Gaetani, G. Persico, A. Mora, V. Dossena, C. Osnaghi, “Impeller-Vaned Diffuser Interaction in a Centrifugal Compressor at Off Design Conditions” J. Turbomach. 134, 061034 (2012)