Advanced turbomachinery blade design
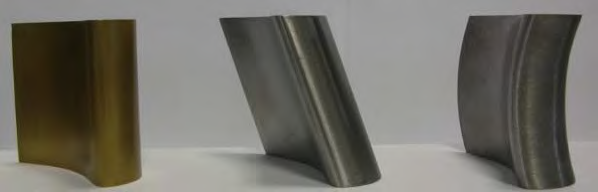
Research activity is addressed to analyze the influence of fully three dimensional design techniques on the performances of turbine blade rows; in particular, 3D design can be used to control the spanwise blade load distribution and thus the radial outlet angle uniformity.
Since the use of linear cascades (Blow down wind tunnel)allows to simplify the phenomenological study, three set of linear cascades (straight, leaned, bowed) obtained by stacking the same 2D profile have been investigated for several operational conditions.
Both pressure distributions inside the passage and on blade surfaces influence discharge angle changes along the blade height, evidencing heavy variations according to the blade loading distribution. Moreover a deep look into the pressure distribution inside the blade passage, achieved by means of detailed numerical simulations, allowed to give a new interpretation of the flow path throughout the channel.
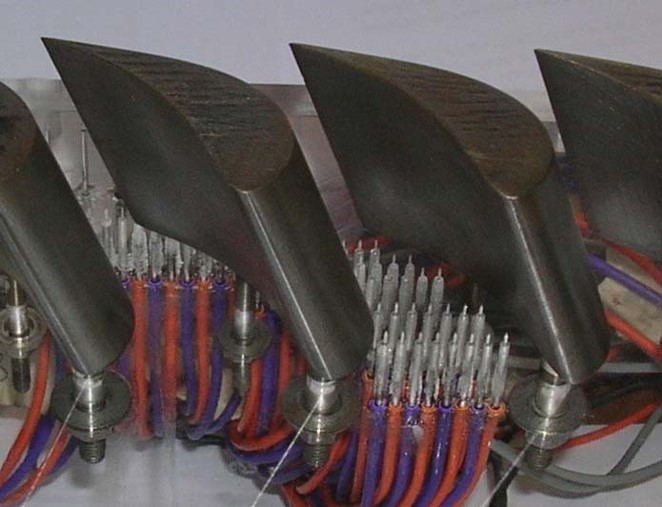
-
3-D blade design effects on the flow field characteristics
-
Downstream of the channel (Experimentally and Numerically)
-
Blade loading (Experimentally and Numerically)
-
Inside the channel (Mainly Numerically)
-
Sensitivity analysis with respect to lean angle and aspect ratio
-
Interpretative key of the flow behaviour throughout the passage
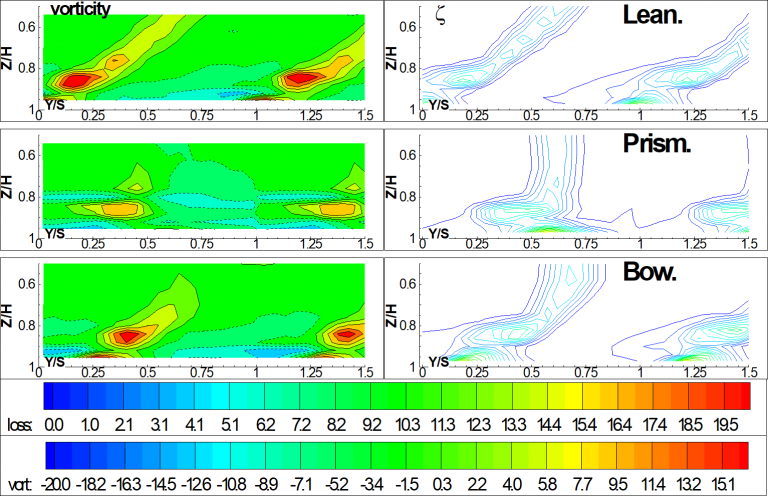
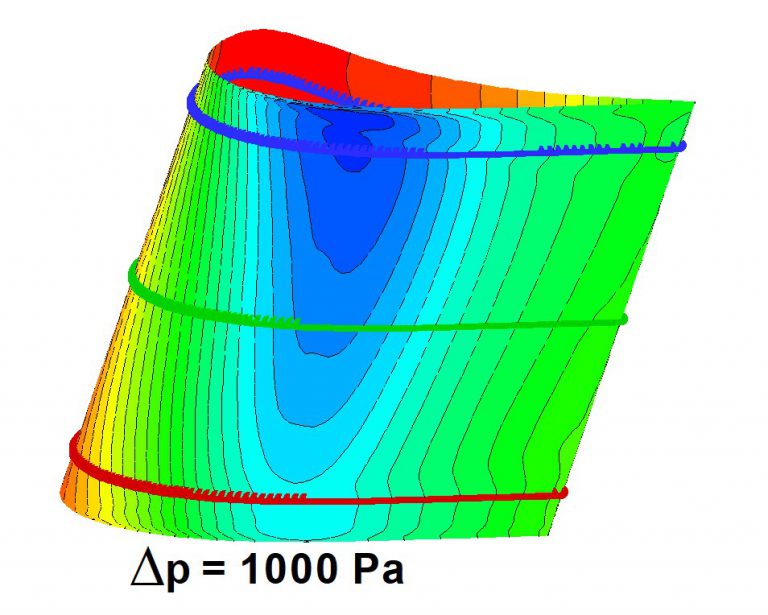
Once a simplified model for the 3D geometry was defined, the activity was focused on actual annular configurations. A new fully 3D stage (figure 6) was designed and optimized by means of a wide CFD investigation. The final design was manufactured and installed in the Low Speed Test Rig of LFM. As a reference case, a standard prismatic vane row was also installed and deeply analyzed in the same facility.
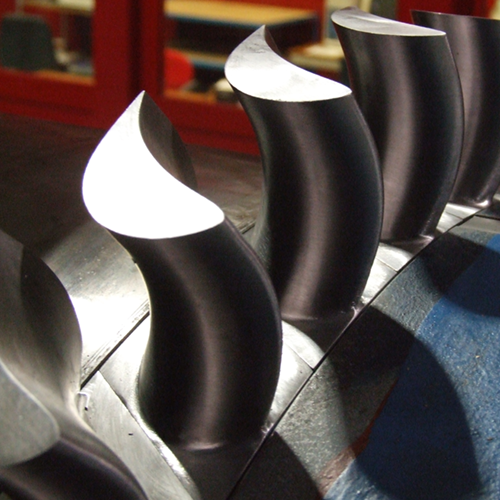
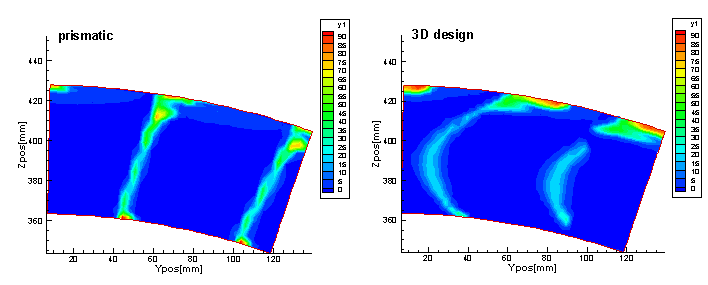